Agenda
Factory tour, keynotes and panels by experts from industry and research
Wednesday, November 20, 2024
4:00 - 5:00 pm
Guided Tour: Karlsruher Forschungsfabrik - Research Factory for AI-integrated Production
Practical research and real manufacturing processes: This is what the Karlsruhe research factory for AI-integrated production is all about. The Fraunhofer Institutes IOSB and ICT and the wbk Institute for Production Technology are involved.
One component of the research is automated production processes for battery cells. This can be experienced on a pilot line. During a guided tour of the factory, participants learn details about the practical production facilities and details about the research into battery cells.
Fotos: © Fraunhofer IOSB / indigo, © KIT, Amadeus Bramsiepe
2. Photo f. l.: Daniel Vieser, architectural photography, Hildesheim/Karlsruhe
from 7:00 pm
Networking Dinner on the evening prior to the »Battery Manufacturing Day«
Enjoy a relaxed dinner in the restaurant of the conference venue ACHAT Hotel Karlsruhe City with participants, speakers and partners of the Battery Manufacturing Day. A short keynote speech will set the tone for the evening. Claus-Peter Köth, Editor-in-Chief of »Automobil Industrie« and Benedikt Hofmann, Editor-in-Chief of MM MaschinenMarkt, will be the welcoming speakers.
Thursday, 21 November 2024
8:00 - 9:00 am
Check-in & Welcome Coffee
ACHAT Hotel Karlsruhe City
9:00 - 9:05 am
Opening
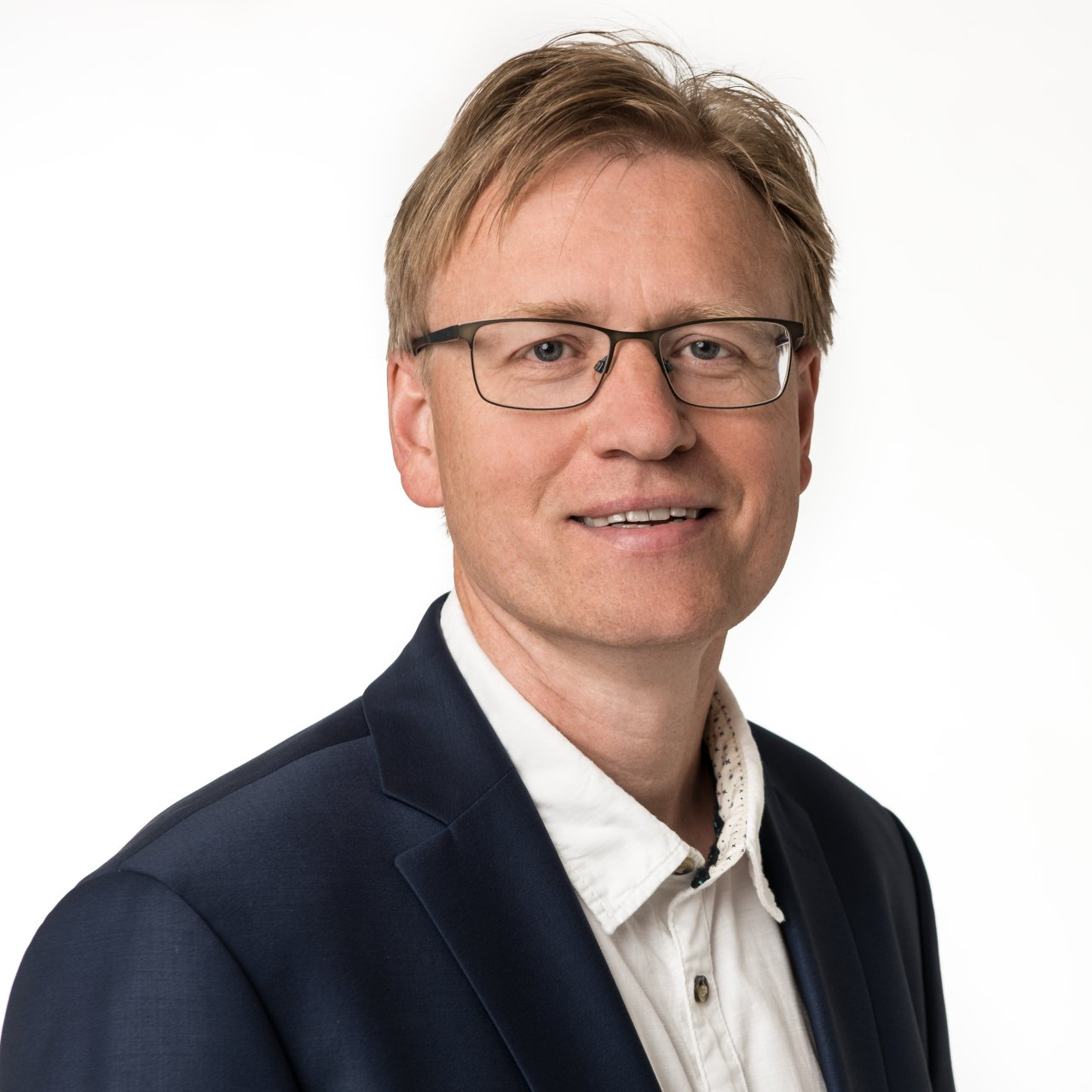
Claus-Peter Köth
Editor-in-Chief »Automobil Industrie«
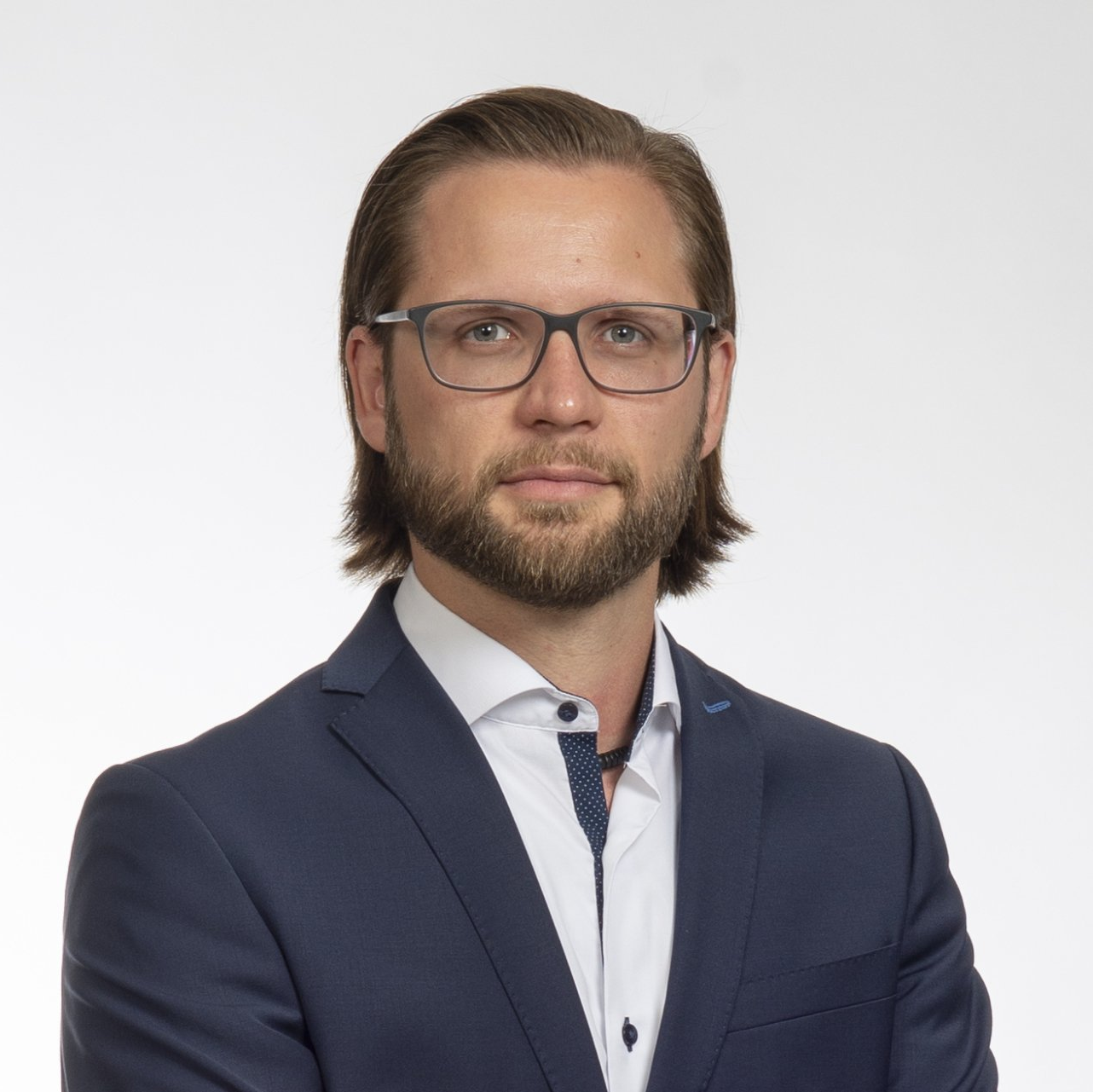
Benedikt Hofmann
Editor-in-Chief MM MaschinenMarkt
9:05 - 9:30 am
Keynote
High voltage systems manufactured by Audi
learn more about the lecture
Audi is expanding its range of fully electric vehicles with the Audi Q6 e-tron and A6 e-tron model families. The models are based on the Premium Platform Electric (PPE). The technical basis of the platform is a completely newly developed drive portfolio consisting of high-voltage batteries and electric drives. The high-voltage batteries play a decisive role in charging performance and range, but also in vehicle weight. Audi is therefore focussing on the use of the latest technologies in cell chemistry for even better energy density. The continuous further development of high-voltage storage systems and electric drives also poses new challenges for production. Audi therefore relies on close cooperation between development and production for new technologies - from day one.
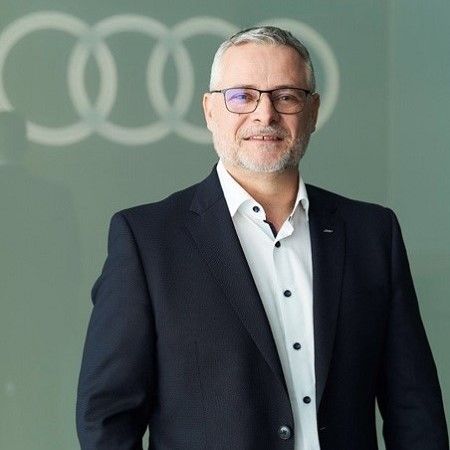
AUDI AG
9:30 - 9:55 am
Challenges in the industrialisation of lithium-ion batteries in the automotive industry
learn more about the lecture
The industrialisation of batteries in Europe presents manufacturers with considerable strategic and operational challenges. The latest announcements and developments regarding projects by cell and pack manufacturers in Europe illustrate the complexity and volatility of such projects.
This presentation will provide practical insights into the key challenges facing battery manufacturers today and present solutions for successful industrialisation in a dynamic market environment. P3, a leading international consulting firm with extensive experience in electromobility and industrialisation, analyses key influencing factors in the development and planning process and presents practical solutions.
The P3 group, founded as a spin-off of the Fraunhofer Institute at RWTH Aachen University, contributes its many years of expertise from international projects in the automotive and energy industries as well as the public sector. With a team of over 1,800 specialists worldwide, P3 offers sound insights and innovative approaches for the successful industrialisation of battery technologies in Europe.
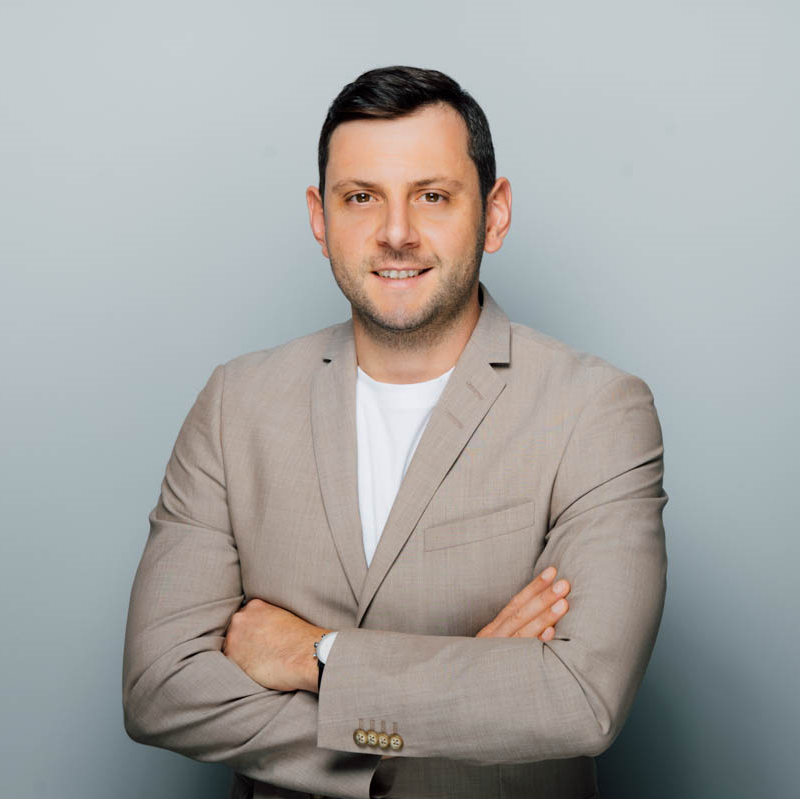
P3 Group
9:55 - 10:20 am
The Karlsruhe Research Factory as a development environment for battery technologies
learn more about the lecture
The description will follow shortly.
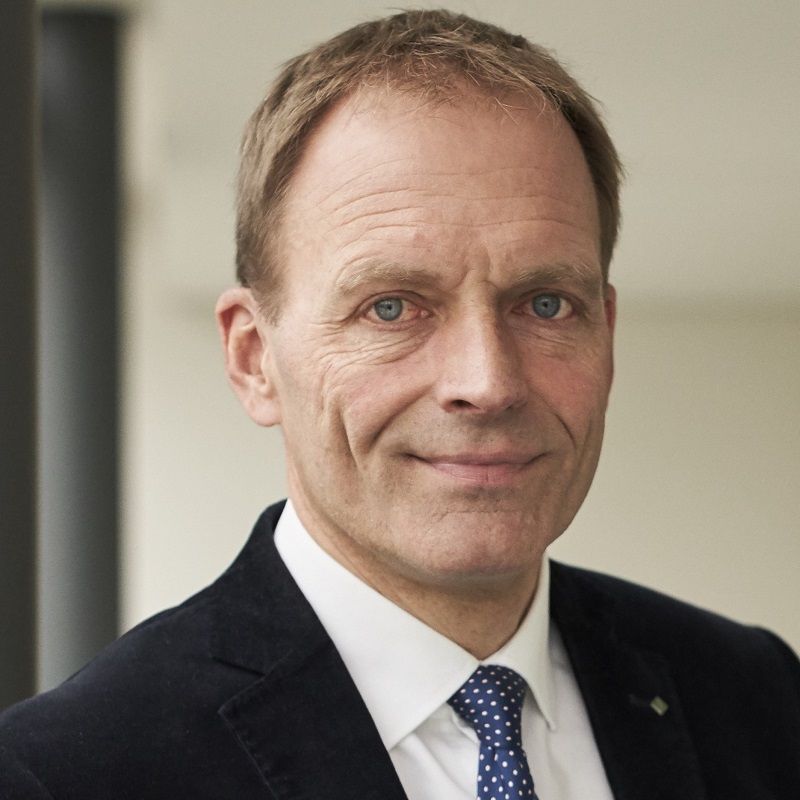
Fraunhofer IOSB
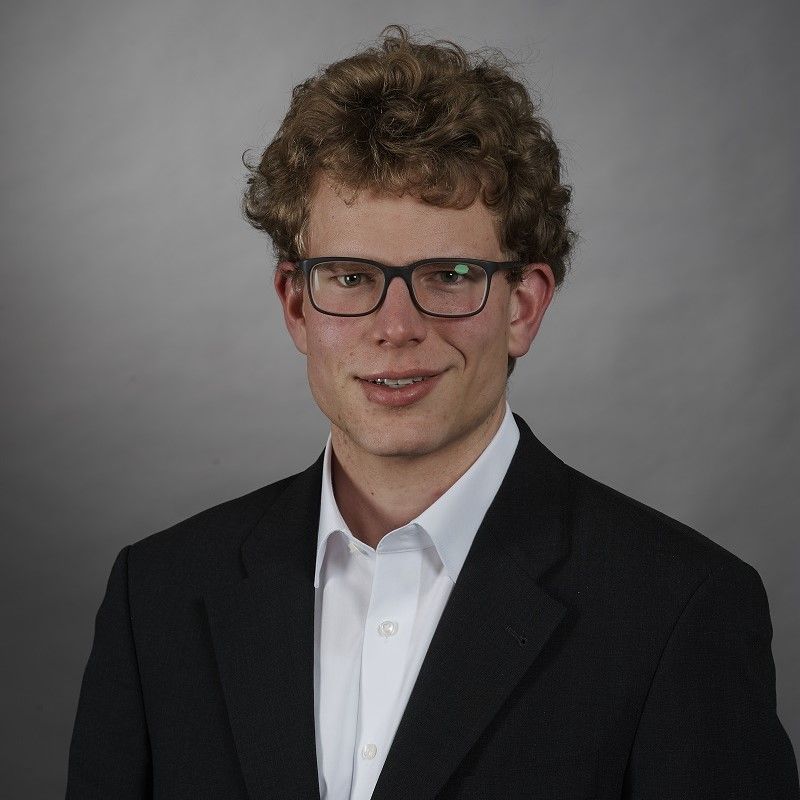
Institute of Production Engineering (wbk) at the Karlsruhe Institute of Technology (KIT)
10:20 - 10:45 am
Energy-efficient micro-environments for battery production
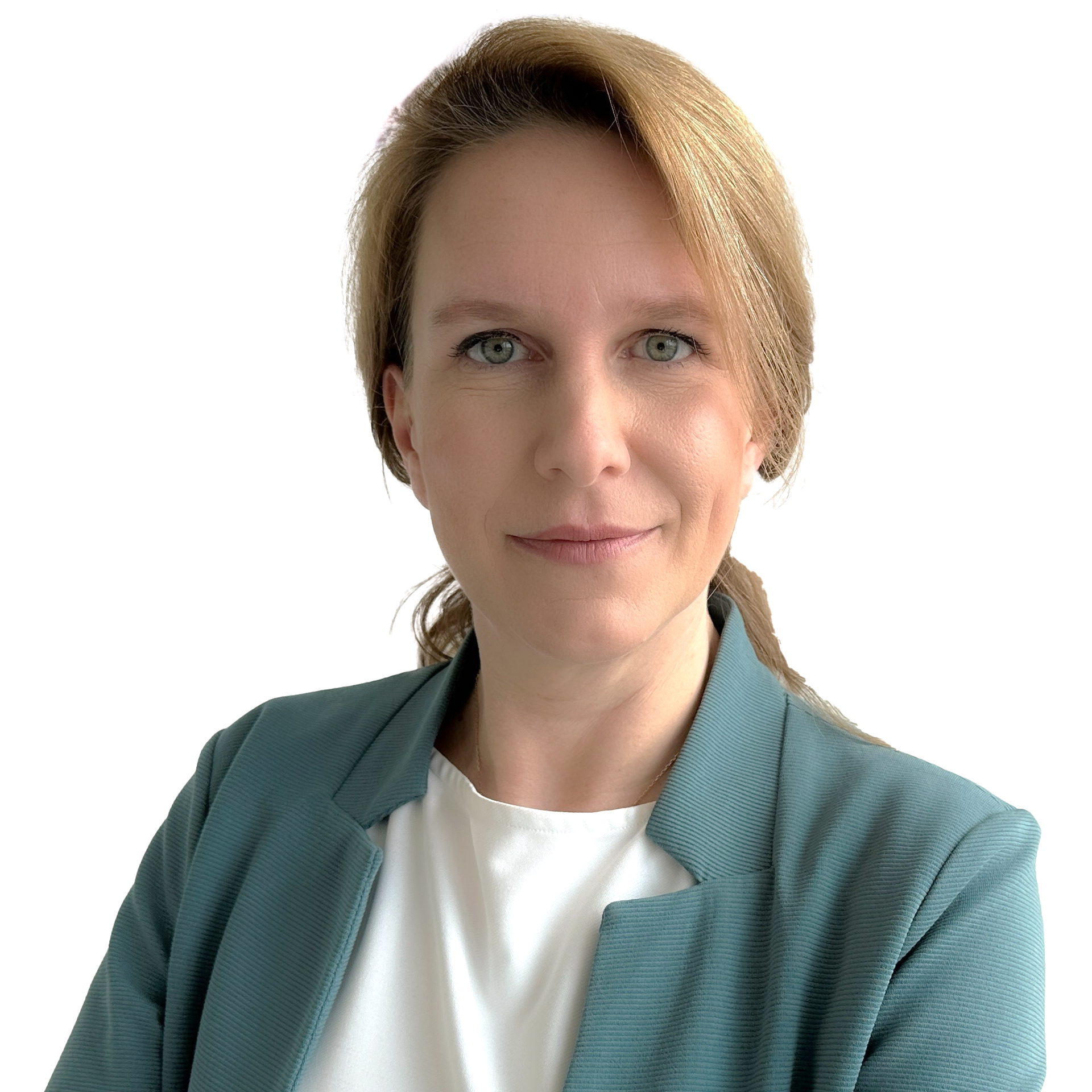
Exyte Technology GmbH
10:45 - 11:20 am
Coffee break
Meet & Talk at the exhibition
11:20 - 11:45 am
Handling of battery components: Processes, fire protection and packaging using a practical example
learn more about the lecture
The rapidly developing technology associated with battery modules for e-mobility requires automation systems to be quickly adapted to the new challenges in this industry.
In his presentation, Stefan Maier explains how he achieves precisely this with his company. In his presentation, Stefan Maier provides insights into the production of a battery cover from an automation perspective. In recent years, his company, ROBOT-TECHNOLOGY, has specialised in the technological production processes for manufacturing battery covers in electric vehicles and in the various production processes in the field of battery cell handling.
Topics of the presentation:
- Technological production processes in the manufacture of a battery cover for e-mobility
- Fire protection systems for battery modules
- Production processes in the field of battery cell assembly.
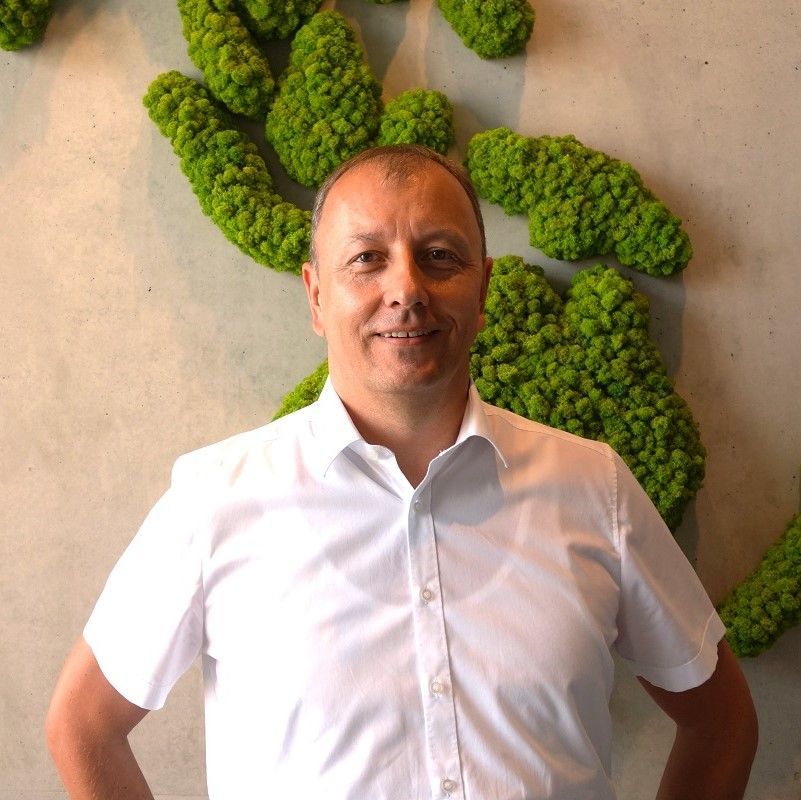
Stefan Maier
ROBOT-TECHNOLOGY GmbH
11:45 - 12:10 am
European mechanical and plant engineering on the way to becoming a supplier of gigafactories for battery production
learn more about the lecture
- Current market overview of battery cell production from the perspective of mechanical and plant engineering
- Schuler's entry into the battery cell production sector
- Current challenges in the battery manufacturing market environment
- Important success factors as a machine and plant manufacturer
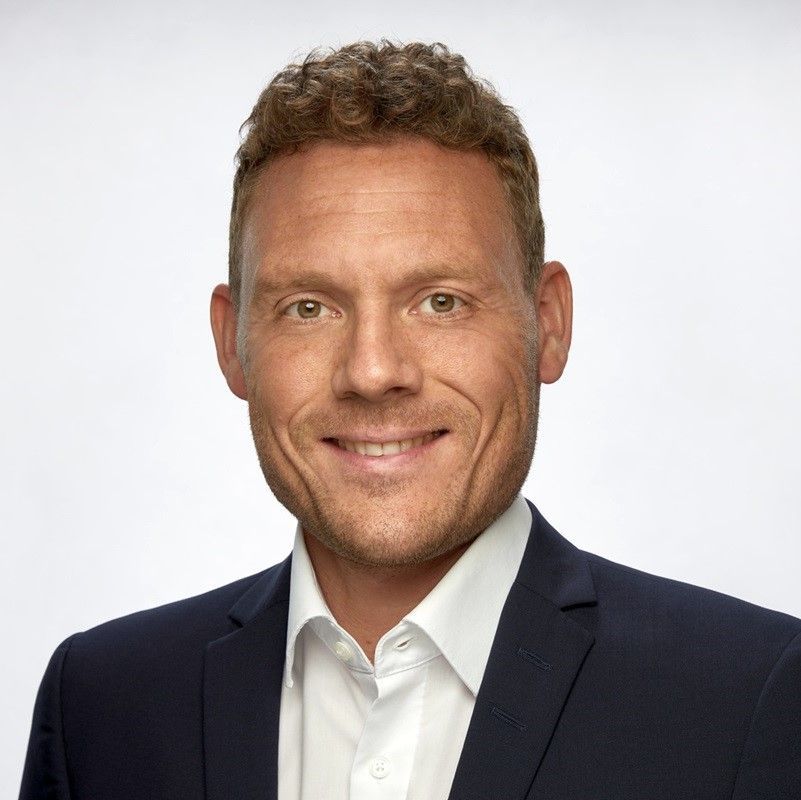
Schuler Pressen GmbH
12:10 - 12:35 pm
Exhibition tour
Time for questions to the exhibitors
12:35 - 1:45 pm
Lunch break
Meet & Talk at the exhibition
1:45 - 2:25 pm
Startup-Session
Startups present innovative products or services
In 3-minute pitches, the speakers have the opportunity to present themselves on the podium. Each presentation concludes with a short Q&A session with the audience.
2:25 - 2:50 pm
Battery production 4.0 - with digital technologies for intelligent production
learn more about the lecture
The presentation will show how Schuler, as a supplier of innovative production systems for battery production, has developed a digitalisation solution for production in cooperation with GEC (Schuler Digital Suite). Here in particular and especially for battery production of great importance, the topic of detailed production documentation for seamless component tracking (traceability), including automated serialisation of components. This is an important aspect when it comes to the digital battery passport. In addition, GEC will show which valuable solution modules can be offered along the battery life cycle in the Group network with Rittal and EPLAN - from engineering to battery production, battery operation in the field and the recycling process.
Focus of the presentation:
- Solution expertise for automated battery production
- Digitalisation modules for intelligent production
- Serialisation and component tracking (Track&Trace)
- Solution modules along the battery life cycle
2:50 - 3:15 pm
Opportunities for battery suppliers through collaborative DCM according to the Catena-X standard
learn more about the lecture
Catena-X aims to create end-to-end networking and secure data exchange along the automotive value chain.
This presentation will introduce the data ecosystem and highlight how it supports specific use cases for optimising the supply chain. The focus will be on the "Demand and Capacity Management" (DCM) use case, which enables efficient coordination of demand and capacity along the supply chain. The example of batteries is used to show how forward-looking planning can avoid bottlenecks and improve resource efficiency.
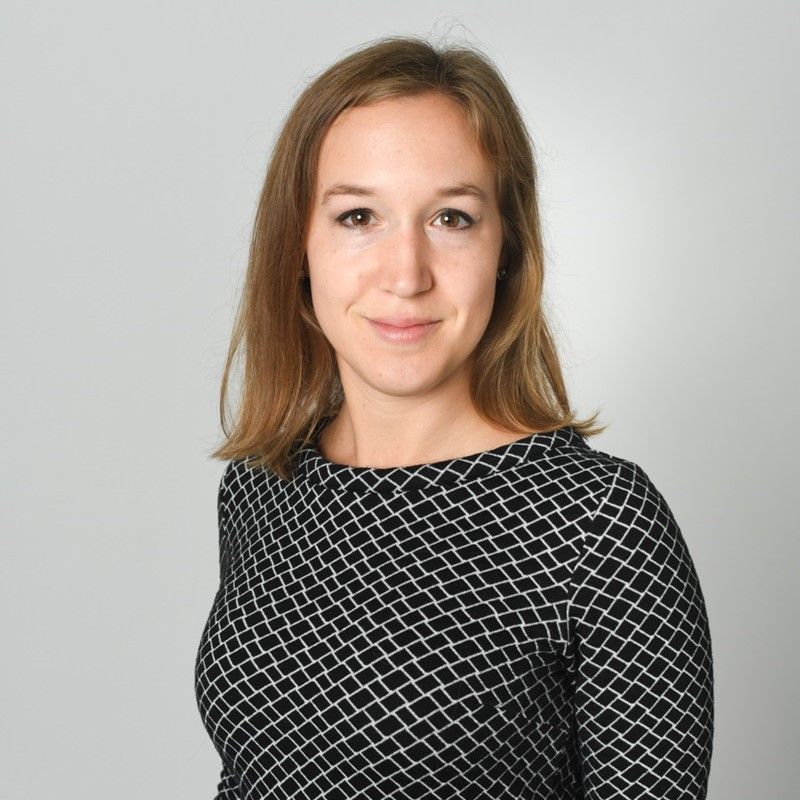
CatX Service GmbH
3:15 - 3:45 pm
Coffee break
Meet & Talk at the exhibition
3:45 - 4:10 pm
Laser-based recycling of lithium-ion batteries
learn more about the lecture
The global mobility revolution is gathering pace. Gigafactories for the production of lithium-ion batteries are being ramped up around the world. Currently, the focus is primarily on the efficient and sustainable production of high-voltage storage systems. In the long term, however, the recycling of traction batteries is a decisive factor for the European battery industry in order to utilise the critical and scarce raw materials as part of a circular economy. Various technologies and strategies are currently being researched for this purpose. This presentation will focus in particular on the potential applications and opportunities of laser technology for the recycling of traction batteries.
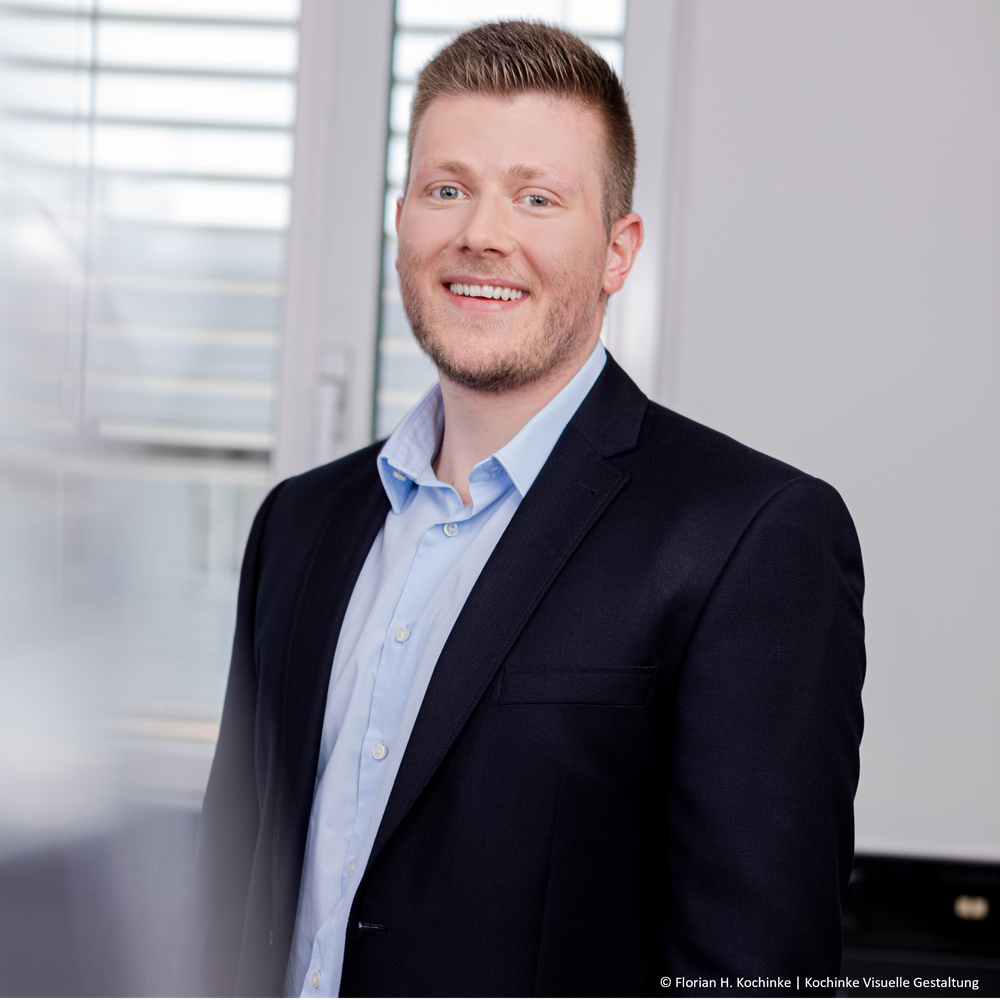
TRUMPF
4:10 - 4:35 pm
Flexible dismantling concepts for batteries are an important cornerstone for sustainability and material independence
learn more about the lecture
Europe's lack of autonomy in battery production jeopardises the future growth of its electromobility and energy sector. Further development of the battery recycling infrastructure is key to securing the supply of raw materials. Automating the sorting and dismantling of batteries is a seemingly small but crucial piece of this puzzle. Image processing and sensor technologies are combined with data analysis and artificial intelligence to create a powerful solution that can reliably identify the respective battery type. Robots also perform dangerous tasks such as opening, discharging and dismantling batteries without putting people at risk.
4:35 - 5:00 pm
Automated testing of battery packs - efficiency and reliability in quality assurance
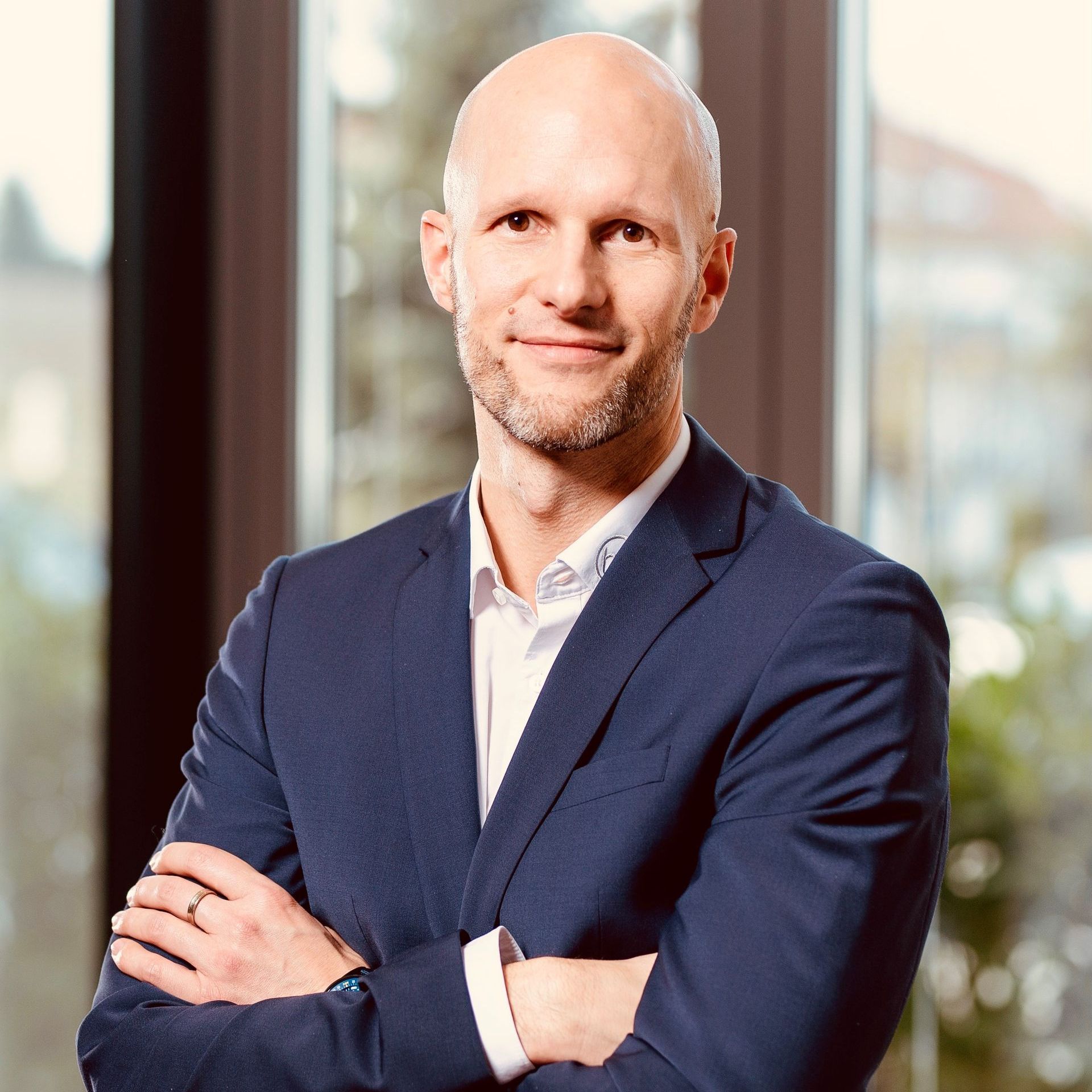
Hahn Automation Group
4:55 - 5:00 pm
Summary and end of Battery Manufacturing Day